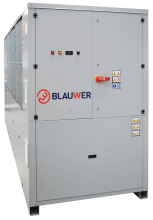
Когда речь идет о конечном качестве полимерной продукции, мелочей не бывает. В полной мере это касается и вспомогательного оборудования, к которому относятся и термоконтроллеры. Тем не менее, случаются ситуации, когда переработчики полимеров даже не знают о назначении этих приборов.
Назначение и возможности
В наши дни трудно представить себе производство изделий из того или иного типа
полимера, при котором не был бы необходим контроль за температурой рабочих
узлов оборудования. Промышленные термоконтроллеры сегодня активно используются
в производственных процессах и являются их неотъемлемой частью. По принципу
действия эти приборы делятся на аналоговые и цифровые. При этом приборы
последнего поколения отличаются компактностью, простотой установки и
обслуживания. Их применение – гарантия того, что процессы, где температурный
режим принципиально важен, будут находиться под контролем и протекать в нужном
режиме. Особенно это касается производства, где требуется повышенная точность
регулирования, а именно литье под давлением при поддержании температуры
пресс-форм или экструзионно-выдувном формовании.
Правильно работающий термоконтроллер – это минимальные затраты
электроэнергии и минимальное количество бракованных изделий. Термоконтроллер
позиционируется как вспомогательное оборудование, которое обычно поставляется в
комплекте вместе со всей производственной линией и входит в комплект под той же
торговой маркой, что и все оборудование. Хотя отдельные узлы его могут
поставлять и другие производители.
Изначально термоконтроллеры отображают и контролируют величину электрического
сигнала от температурного или другого аналогового датчика. После обработки
данных процессором контроллер путем подачи сигналов на электромагниты
корректирует работу исполнительных устройств, как-то: приводного двигателя
шнека, нагревательных элементов через модульный термоконтроллер, положение
различных клапанов и задвижек и т.п. При этом температура в охлаждающих
контурах литьевых форм или валов должна быстро достигать установленных
значений, иначе технологический процесс может быть нарушен.
Точность работы этой автоматики в конечном счете влияет на важнейшие свойства изделия: механическую прочность, качество поверхности, точность размеров, отсутствие коробления. Если температура пресс-формы превышает заданную, то электронная система управления открывает магнитный клапан в системе подачи воды в теплообменник, куда поступает холодная вода и забирает тепло, полученное термостатической жидкостью в пресс-форме. При этом в современном контроллере можно не только выставлять параметры температуры под конкретное изделие, но и загружать готовый набор параметров (рецепты) для контроллера под каждый вид продукции, вести архив данных, выводить предупредительные и аварийные сигналы.
Юрий Шовгенюк, замкститель директора по техническим вопросам ООО «МикРА» (Украина, Киев): «Полимерная промышленность – один из основных потребителей терморегуляторов. По нашим оценкам, до 30 % производимых нами приборов используются в оборудовании для производства и переработки пластмасс. Задача терморегулятора в таком оборудовании – максимально точно поддерживать требуемую температуру полимера в процессе его обработки.
Первичные датчики, в качестве которых чаще всего используют термопары или термометры сопротивления, выдают на терморегулятор сигнал, пропорциональный температуре в рабочей зоне в данный момент. Терморегулятор должен управлять системой нагрева (а в некоторых задачах и системой охлаждения) таким образом, чтобы в любой момент, вне зависимости от внешних воздействий, инерционности системы и ее других характеристик, обеспечить требуемую температуру. Чаще всего в подобных системах используют пропорционально – интегрально – дифференциальные (ПИД) регуляторы, так как именно они способны обеспечить наибольшую точность регулирования в таких сложных условиях.
В зависимости от количества точек, в которых необходимо поддерживать
температуру, требований надежности и ремонтопригодности применяют одно- или
многоканальные терморегуляторы. Если в процессе работы требуется периодически
изменять температуру в каждой точке системы, собирать и сохранять для анализа
параметры техпроцесса, то используют системы управления на основе контроллеров
объединенных в сеть передачи данных.
В оборудовании для литья изделий из пластмассы в последнее время все чаще
используют горячеканальные пресс-формы. Для таких сложных и точных механических
изделий важно равномерно и согласованно прогревать каждую точку детали. Поэтому
кроме системы управления температуры собственно термопластавтомата приходится
разрабатывать и изготавливать отдельную систему регулирования температуры для
каждой конкретной пресс-формы».
Разновидности
Подбор ТК под конкретное производство – технически достаточно непростая задача.
Ведь сегодня рынок предлагает большой выбор термоконтроллеров, различающихся по
принципу теплопереноса и типу применяемого хладоносителя. Для подбора нужно
знать все особенности и параметры производства, хорошо знать физику и
технологию конкретного процесса. Тем более что термоконтроллеры намного сложнее
совершеннее и разнообразнее термостатов, которые являются скорее инструментом
поддержания температуры, нежели командным центром для ее регулирования.
Задача термолегуляротов состоит лишь в том, чтобы иметь достаточную тепловую
мощность для нагрева теплоносителя и достаточную мощность охлаждения для
быстрого снижения температуры в охлаждающих контурах. Специалисты различают
стандартные терморегуляторы, регуляторы процесса, модульные регуляторы,
многоканальные регуляторы температуры и т.д. Существуют и другие принципы
деления на типы. Например, термостаты на основе воды, напорной воды и
масла-теплоносителя в температурных диапазонах до 300 °С. Они разработаны для
поддержания равномерной температуры литьевых пресс-форм и форм для литья под
давлением, а также валков, экструдеров и смесителей.
Среди параметров отбора может быть:
1. Максимальная температура в охлаждающих контурах. Если температура в
охлаждающих каналах не более 180 С, в качестве теплоносителя используется вода.
Если максимальная температура в охлаждающих контурах свыше 200 С , то
хладагентом может быть только масло.
2. Максимальная мощность нагрева теплоносителя имеет главное значение при
запуске холодного оборудования. Чем сильнее нужно разогреть литьевую форму или
вал за малое время, тем больше нужна мощность по нагреву. При некоторых
процессах мощность нагрева может быть важной характеристикой и внутри
производственного цикла.
3. Мощность охлаждения – один из самых важных критериев. Чем больше мощность
охлаждения, тем быстрее упадет температура в охлаждающих каналах литьевой
формы. При правильном выборе ТК цикл литья на ТПА может быть минимальным, и
значит, литьевая машина будет использоваться на максимуме своих
возможностей.
4. ТК с открытым контуром охлаждения. Эти приборы могут не иметь теплообменника
и работать в режиме прямого охлаждения. В этом варианте вода из системы
напрямую поступает в каналы охлаждения и достаточно эффективно отводит тепло от
контуров пресс-форм. Достоинство этой конструкции – высокая скорость отвода
тепла при малых расходах электроэнергии. Минус системы – высокие требования к
качеству подготовки воды.
5. ТК с Закрытым контуром работают в режиме косвенного охлаждения. Вода из
системы поступает в теплообменник и там отнимает тепло от воды или масла. Вода
или масло циркулирует в независимом контуре, и охлаждающие каналы замкнуты на
этот контур. Достоинство системы – вода может быть специально подготовленной и
минимально воздействовать на контура пресс-формы, реже придется проводить
очистку каналов. Но, к сожалению, скорость охлаждения ниже, чем у термостатов с
открытым контуром, больше время цикла.
Многоканальные ТК легко монтируется и обеспечивает одновременное управление нагревом либо охлаждением. Регуляторы оснащены различными выходами управления (выходом напряжения, аналоговым выходом, выходом с NPN-транзистором), а их параметры могут настраиваться с помощью ПК или специального программатора.
Характерна для прибора и высокая скорость опроса – до 200 мс по всем 8-10-ти
каналам.
Современные системы имеют возможность отдельного ввода рабочих параметров для
каждого контура термостатирования. Количество контуров может достигать 12 .
Также система может обеспечить выравнивание разности температур между смежными
каналами. Имеется программа запуска для предварительного нагрева пресс-формы,
таймер с программой на рабочую неделю и возможность сохранения алгоритма
заданной температуры для различных пресс-форм.
Максим Баценко, директор представительства IBC SISTEMS (Украина): «Продукция IBC SISTEMS вполне конкурентоспособна и на украинском и на международном рынке. Вся линейка оборудования – это итальянская продукция. Поэтому мы не очень в курсе, какую долю рынка занимают здесь украинские и российские приборы. Конечно, на рынке есть и европейское и азиатское, оборудование..
При этом компании, которые имеют достаточно большой опыт, стараются брать импортное оборудование. Да по большому счету у них просто нет альтернативы. В свое время мы рассматривали возможность производства термоконтроллеров в Украине и столкнулись с рядом чисто технических сложностей. Выяснилось что собирать термоконтроллеры здесь, даже имея на него всю техническую документацию, не слишком то выгодно. Прибор получится не намного дешевле, в то же время некоторые детали изготовить вообще практически нереально. Например, теплообменник в контроллере закрытого типа никто не взялся делать в Украине».
Производители и рынок
Выбор подходящего ТК непрост еще и по причине богатства выбора. Термоконтроллер
нельзя назвать простым устройством, тем не менее, он проще и существенно
дешевле по сравнению с другими компонентами производственной линии и по
стоимости соизмерим с компьютером специального назначения – да по сути он
таковым и является. Поэтому производители такого оборудования есть практически
в любом технически развитом государстве.
Одноканальный ТК российского производства может стоить 150-300у.е.
Многоканальный с числом каналов 8-10, конечно, дороже но и это не слишком
дорого – на уровне 300-500У.е. Но цена зависит и от точности, и от имени
производителя. Даже одноканальный регулятор высокой точности и высокой скорости
реакции может стоить 800-1000 у.е. Немецкое или итальянское оборудование может,
конечно, стоить и на порядок дороже.
Общеизвестны мировые лидеры в данной отрасли – это ЮМО, OMRON, PIKTRONIX. На
внутреннем рынке СНГ присутствуют контроллеры PIOVAN (Италия) WHITMAN Австрия
MOTON (Германия). Аутоникс (Корея), Дельта (Тайвань).
Более чем достаточно производителей ТК в России. Это такие компании, как ООО
«Овен» Элемер, Термодат, Теплоприбор, МЗТА, Вибратор, Данатерм, НПП Автоматика,
Сенсорика, ФЭА, Контравт и многие другие. Всего несколько десятков, хотя
безусловным лидером, которому трудно составить конкуренцию, является именно
«Овен». В Украине производством термоконтроллеров занимается ООО «МИКРА»
(Киев), Scroll (Ивано-Франковск), «Промприбор» в Житомире, Терра в Чернигове,
филиал российского Овна в Харькове и еще несколько. В целом около десятка.
Что касается китайских контроллеров, то скепсис по отношению к ним очень велик.
В России их не покупают даже на Дальнем Востоке, где они еще дешевле из-за
близости доставки. В то же время не редки случаи, когда на импортные
производственные линии ставят контроллеры российского или украинского
производства, поскольку они по ряду показателей вполне конкурентоспособны.
Единственной проблемой является то, что заявленных дилерами моделей вполне
может не оказаться на складе.
Максим Крец, начальник ассортиментного направления КИПиА компании ОВЕН
(Россия, Москва): «Далеко не все производители полимерных изделий пользуются
импортным оборудованием, хотя если говорить о производителях локальной
автоматики, то доля импортного оборудования здесь, конечно, подавляющая. Тем не
менее, в России есть и отечественные производители термопластавтоматов,
экструдеров и т.д. Отношение к отечественному продукту зачастую предвзятое, но
на поверку оказывается, что с отечественным производителем иногда работать
проще, и причин здесь достаточно:
вполне достойное качество;
цена ниже, чем у европейских аналогов;
более короткие сроки поставки;
наличие техподдержки и сервиса.
Влияют также на ситуацию и ряд целевых госпрограмм, в силу которых поставщики
ограничены в применении импортного оборудования. И этот факт способствует
продвижению отечественной продукции.
Очень разные цифры и в ценовом ряду оборудования. У европейцев есть так
называемые «топовые линейки» – они дороже в десятки раз. Линейки приборов
среднего уровня дороже примерно в 3-5 раз, продукция японского производства – в
1,5-2 раза, корейского – есть и дешевле. Китай даже не обсуждается ввиду
неприемлемого качества оборудования данной категории...
Проблемы с заменой вышедшего из строя оборудования, в принципе, возможны, хотя они носят преимущественно технический характер. При необходимости осуществления оптимальной замены трудность, скорее всего, состоит в том, чтобы правильно сформулировать задачи, которые должна выполнять автоматика. А сама реализация вопросов не вызывает.
Конкурентоспособных фирм, производящих ТК, в России достаточно. Это Элемер, Термодат, Теплоприбор, МЗТА, Вибратор, Данатерм, НПП Автоматика, Сенсорика, ФЭА, Контравт и многие другие. Противостоят им такие известные мировые лидеры, как Юмо (Германия), Омрон (Япония), Аутоникс (Корея), Дельта (Тайвань)».
Алексей Балыкин, Директор ООО «Ситрона-КИП» (Россия): «Наша компания – непосредственный производитель оборудования, и это оборудование в достаточной мере востребовано предприятиями России, работающими в полимерной промышленности. Мы же производим готовые к эксплуатации контроллеры с использованием приборов и датчиков, производимых на ООО «Овен». Что касается конкуренции в этой области на российском рынке, то здесь ситуация диктуется тем, что если кто-то готовит производство с нуля, то велика вероятность того, что вся производственная линия будет укомплектована термоконтролерами того же производителя, что и основная производственная линия.
Но я бы не сказал, что импортные приборы полностью доминируют на российском рынке. Это объясняется как существенной разницей в стоимости, так и сложностью в обслуживании. Если импортный термоконтроллер выходит из строя, то его ремонт в России сопряжен с немалыми сложностями. В принципе, ТК иностранного производства может быть отремонтирован и в России, но это требует существенно большего времени, особенно если речь идет о замене деталей, на доставку которых требуется много времени. Потребляются наши контроллеры, конечно же, преимущественно в России, поскольку предприятий по переработки пластика в других странах СНГ значительно меньше. За последнее время мы помним только две поставки ТК в Украину и Белоруссию».
Степень востребованности и проблемы эксплуатации
Изначально контроллер как оборудование покупается не так часто, как этого
хотелось бы поставщикам и производителям. Это происходит, когда создается новое
производство или на действующем что-то выходит из строя. Контроллер может
работать годами вплоть до морального устаревания оборудования, если его
правильно эксплуатировать. Увы, неквалифицированное вмешательство может
угробить любой контроллер. Как сообщил «ПД» Юрий Шовгенюк, большинство
приборо,в которые возвращаются в ремонт, были повреждены или сожжены
неквалифицированными действиями персонала. К сожалению (а может, и к счастью
для поставщиков и производителей), длительность срока службы контроллера более
всего зависит от человеческого фактора. Статистика свидетельствует, что 95%
поломок ТК – это результат низкой квалификации эксплуатационников.
Того же мнения придерживается и Максим Баценко: «К сожалению, до сих пор приходится обращать внимание на низкую культуру производства и непонимание многими производителями того, зачем вообще в составе линии нужны термоконтроллеры. У нас все еще сказывается дефицит квалифицированных кадров и низкий уровень культуры производства. И здесь проблемы примерно равные как в России, так и в Украине. Стандартная ситуация – когда о термоконтроллере вспоминают в момент запуска оборудования. Причем чаще всего это происходит на новых литьевых производствах, поскольку для ТПА термоконтроллер желательная, но не обязательная опция. Использование термоконтроллера позволяет уменьшить потери сырья при запуске, улучшить стабильность работы, а также получать более качественные изделия. С экструзией проще – в состав линии термоконтроллеры, как правило, включены».
Крайне нежелательны для этих приборов также броски напряжения в сети, которые типичны для наших предприятий. Из-за этого «летит» точная электроника и выгорают датчики. На промышленных предприятиях работает мощное оборудование, и потому броски напряжения на наших предприятиях – обычное дело. Так что уровнем продаж дилеры в немалой степени обязаны не только неграмотному персоналу, но и нашим энергетикам. А как хотелось бы, чтобы число продаж было обеспечено возрастающими объемами производства…
Константин Егоров
Статья из журнала «Полимеры-Деньги», Август 2011