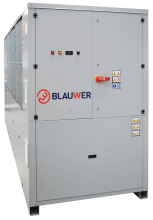
Injection moulding
Injection moulding is the most flexible plastic process, in terms of shape and materials of the produced parts, and the technical specifications are very different from each other.
The range of temperatures is very wide: the mould must be kept at temperatures ranging from 5 °C (fast moulding for thin-wall containers or disposable cutlery and dishes) to 190°C and more (technical components made of PEEK).
Sometimes the application presents conflicting requirements: plastic material must be fluid and hot during injection in order to fill mould cavities completely, cooling must be very quick to increase the productivity and, for crystalline materials moulding time must be long enough for crystallization of the material. It is therefore necessary to work at high temperatures and remove more heat per each kilo of the processed material.
Depending on the process temperature the mould can be directly water-cooled by the chiller or through thermo-controllers. Temperature control can be done using water as a heat-carrier (up to 90 °C), pressurised water (up to 140°C or 160°C) or diathermic oil (up to 330°C). Utilization of temperature control units allows to control temperature more accurately, to increase cooling speed and fluid pressure (multi cavity moulds).
Regardless of the fact whether the mould works at low or high temperature during moulding the mould should be cooled. It is often necessary to cool both the hydraulics of the press as well to avoid problems connected with hydraulic oil overheat and seals and other parts of the press. In most of these machines the transfer of the mechanical working power happens via the hydraulic oil. Part of the power input is transferred as heat to the hydraulic oil which consequently needs to be cooled. freqency shifters, pumps, inverters and other technical solutions can significantly reduce the total heat load and therefore the necessity of cooling. While using electrical machines there is no need of cooling at all.
Extrusion
Extrusion is mostly suitable for manufacturing “long” products (film, foil and profiles) and it can provide high productivity for each single line. Extrusion lines consist of a fairly standard plastification system and a part of cooling the extruded product that can be completely different from one line to another. In the plasticizing group it is necessary to control the temperatures of the various sectors of the screw(s) (with air, water or oil). It is also necessary to cool the oil in the motor gear and the feeding throat. What concerns the extruded product itself, depending on the product, it can be necessary to cool dies, calibrators, calenders, vacuum pumps and cooling baths. Since the extruded material is processed at lower temperature than in injection moulding, the total heat load per kilo of product (for its cooling) is lower. As the process is continuous, there is less heat transfer between different moving parts and therefore less cooling is required for various gears.
Extrusion-blow moulding
Extrusion-blow moulding is used to produce bottles and similar hollow thin-wall pieces. Plastic material in the shape of a preform is mechanically stretched and blown with compressed air to adhere to the mould walls and take the final shape of the bottle. Blow moulding is used, starting from a flask (an extruded cylinder of plastic), to directly blow it inside the mould (without mechanical stretching). Blow moulding can be used to produce bottles, bins, cans, tanks, manifolds air ducts etc. Normally most of the cooling capacity is required for cooling the mould where the product is quickly cooled to take its final shape. Other zones and parts to be cooled depend on the type of plastic process and method of moulding (injection or extrusion). Normally it is necessary to provide cold water at 8 ÷ 12 °C. Such low temperature causes a lot of moisture to condensate on the mould(s) especially during hot season, resulting in problems to the appearance of the blown pieces. This problem can be reduced by increasing the mould temperature (therefore it leads to a longer moulding cycle and reduced productivity) or installing a mould dryer and possibly closing the moulding area in a confined “chamber”.
Thermoforming
Thermoforming is a way of moulding from a plastic film (sheet) with various techniques (pressure or vacuum). Plastic sheet is preheated before moulding or, if the sheet is produced on the same line by extrusion method, preheating is not required – the sheet is used with the temperature at which it is directly taken from the extrusion downstream the calenders. Depending on the product it is held on the mould surface and with a counter-mould it gets the desired shape and dimensions. The mould has to be cooled to fix the shape of the pieces and guarantee the mechanical characteristics and the appearance of the products. If there is a pre-heating station (when it is not in line with the extrusion line) some cooling is also necessary in some parts of it. The cooling power is normally quite low and depends on the productive capacity of the line and power of the heaters.
Recycling
Recycling of plastics requires cooling and temperature control as well as for all plastic production processes. Recycling of plastics or tyre rubber requires cooling of some machines types to prevent dangerous working conditions (risk of fire), guarantees better quality of the product and high productivity.