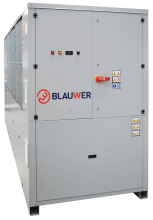
When it comes to the final quality of polymer products, there are no trifles. This fully applies to auxiliary equipment, which includes thermal controllers. Nevertheless, there are situations when polymer processors do not even know about the purpose of these devices.
Appointment and capabilities
Today it is difficult to imagine the production of products from one or another
type of polymer, in which temperature control of the operating units of the
equipment would not be necessary. Industrial thermocontrollers are
actively used today in production processes and are their integral
part. According to the principle of operation, these devices are divided
into analog and digital. At the same time, the latest generation devices
are compact, easy to install and maintain. Their use is a guarantee that
processes where the temperature regime is of fundamental importance will be
under control and proceed in the required mode. This is especially true
for production where increased accuracy of regulation is required, namely
injection molding while maintaining the temperature of the molds or
extrusion-blow molding.
A properly working thermal controller is the minimum cost of electricity and
the minimum number of defective products. The temperature controller is
positioned as auxiliary equipment, which is usually supplied complete with the
entire production line and is included in the package under the same brand name
as all equipment. Although individual components can be supplied by other
manufacturers.
Thermocontrollers initially display and control the magnitude of the electrical
signal from a temperature or other analog sensor. After data processing by
the processor, the controller, by applying signals to the electromagnets,
corrects the operation of actuators, such as: a screw drive motor, heating
elements through a modular thermal controller, the position of various valves
and gate valves, etc. In this case, the temperature in the cooling
circuits of injection molds or shafts must quickly reach the set values,
otherwise the technological process may be disrupted.
The accuracy of this automation ultimately affects the most important properties of the product: mechanical strength, surface quality, dimensional accuracy, lack of warpage. If the mold temperature exceeds a predetermined temperature, the electronic control system opens a magnetic valve in the water supply system to the heat exchanger, where cold water enters and collects the heat received by the thermostatic fluid in the mold. At the same time, in a modern controller, you can not only set the temperature parameters for a specific product, but also download a ready-made set of parameters (recipes) for the controller for each type of product, maintain a data archive, display warning and alarm signals.
Yuriy Shovgenyuk, Deputy Director for Technical Issues, MikRA LLC (Ukraine, Kiev): “The polymer industry is one of the main consumers of temperature controllers. According to our estimates, up to 30% of the devices we manufacture are used in equipment for the production and processing of plastics. The task of the temperature regulator in such equipment is to maintain the required polymer temperature as accurately as possible during its processing.
Primary sensors, which are most often used thermocouples or resistance thermometers, give a signal to the thermostat proportional to the temperature in the working area at the moment. The temperature regulator must control the heating system (and, in some tasks, the cooling system) in such a way that at any time, regardless of external influences, the inertia of the system and its other characteristics, the required temperature can be ensured. Most often, in such systems they use proportional-integral-differential (PID) controllers, since it is they that are capable of providing the greatest control accuracy in such difficult conditions.
Depending on the number of points at which it is necessary to maintain the
temperature, reliability and maintainability requirements, single or
multi-channel temperature controllers are used. If in the process of work
it is required to periodically change the temperature at each point in the
system, to collect and save the technological process parameters for analysis,
then control systems based on controllers integrated into the data transmission
network are used.
In equipment for the molding of plastic products, hot-run molds have been
increasingly used recently. For such complex and precise mechanical
products, it is important to warm every point of the part evenly and
consistently. Therefore, in addition to the temperature control system of
the injection molding machine itself, it is necessary to develop and
manufacture a separate temperature control system for each specific mold. ”
Varieties
Selection of TC for a specific production is technically a rather difficult
task. Indeed, today the market offers a large selection of thermal
controllers, which differ in the principle of heat transfer and the type of
refrigerant used. To select, you need to know all the features and
parameters of production, know the physics and technology of a particular
process. Moreover, thermocontrollers are much more sophisticated and more
diverse than thermostats, which are more a tool for maintaining temperature
than a command center for its regulation.
The task of thermolegulars is only to have sufficient thermal power for heating
the coolant and sufficient cooling power to quickly reduce the temperature in
the cooling circuits. Specialists distinguish between standard temperature
controllers, process controllers, modular controllers, multi-channel
temperature controllers, etc. There are other principles of division into
types. For example, thermostats based on water, pressure water and heat
transfer oil in the temperature ranges up to 300 ° С. They are designed to
maintain the uniform temperature of injection molds and injection molds, as
well as rolls, extruders and mixers.
Among the selection parameters may be:
1. The maximum temperature in the cooling circuits. If the temperature in
the cooling channels is not more than 180 C, water is used as a heat
carrier. If the maximum temperature in the cooling circuits is over 200 °
C, then only oil can be the refrigerant.
2. The maximum heating power of the coolant is of prime importance when
starting up cold equipment. The stronger you need to heat the mold or the
shaft in a short time, the more heating power is needed. In some
processes, heating power can also be an important characteristic within the
production cycle.
3. Cooling capacity is one of the most important criteria. The greater the
cooling power, the faster the temperature will drop in the cooling channels of
the injection mold. With the right choice of TC, the injection cycle on
TPA can be minimal, which means that the injection machine will be used to the
maximum of its capabilities.
4. TC with an open cooling circuit. These devices may not have a heat
exchanger and operate in direct cooling mode. In this embodiment, water
from the system directly enters the cooling channels and efficiently removes
heat from the mold circuits. The advantage of this design is its high heat
dissipation rate at low power consumption. The disadvantage of the system
is high requirements for the quality of water treatment.
5. TCs with a closed circuit operate in indirect cooling mode. Water from
the system enters the heat exchanger and there takes away heat from water or
oil. Water or oil circulates in an independent circuit, and cooling
channels are closed to this circuit. The advantage of the system is that
water can be specially prepared and minimally affect the mold contour, less
often you will have to clean the channels. But, unfortunately, the cooling
rate is lower than that of thermostats with an open circuit, longer cycle
time.
Multichannel TCs are easily mounted and provide simultaneous control of heating or cooling. Regulators are equipped with various control outputs (voltage output, analog output, output with NPN transistor), and their parameters can be adjusted using a PC or a special programmer.
The device is also characterized by a high polling rate - up to 200 ms
across all 8-10 channels.
Modern systems have the ability to separately enter operating parameters for
each thermostat circuit. The number of circuits can reach 12. The
system can also provide equalization of the temperature difference between
adjacent channels. There is a launch program for pre-heating the mold, a
timer with a program for the working week and the ability to save the set
temperature algorithm for various molds.
Maxim Batsenko, Director of the IBC SISTEMS representative office (Ukraine): “IBC SISTEMS products are quite competitive in the Ukrainian and international markets. The entire line of equipment is Italian products. Therefore, we are not very aware of what market share is occupied by Ukrainian and Russian devices. Of course, there are European and Asian equipment on the market ..
At the same time, companies that have quite a lot of experience are trying to take imported equipment. Yes, by and large, they simply do not have an alternative. At one time, we considered the possibility of manufacturing thermal controllers in Ukraine and faced a number of purely technical difficulties. It turned out that collecting temperature controllers here, even having all the technical documentation on it, was not very profitable. The device will turn out not much cheaper, at the same time, it’s almost impossible to make some parts at all. For example, no one undertook to do a heat exchanger in a closed-type controller in Ukraine. ”
Manufacturers and the market
Choosing the right shopping mall is also not easy because of the wealth of
choice. The thermocontroller cannot be called a simple device,
nevertheless, it is simpler and significantly cheaper compared to other
components of the production line and is comparable in cost to a
special-purpose computer - in fact, it is. Therefore, manufacturers of
such equipment are in almost any technically developed country.
A single-channel shopping mall of Russian production can cost
150-300u. Multichannel with the number of channels 8-10, of course, is
more expensive, but it is not too expensive - at the level of
300-500U. But the price depends on accuracy and on behalf of the
manufacturer. Even a single-channel regulator of high accuracy and high
reaction rate can cost 800-1000 cu German or Italian equipment can, of
course, cost and an order of magnitude more expensive.
Well-known world leaders in this industry are YuMO, OMRON, PIKTRONIX. In
the domestic market of the CIS there are PIOVAN controllers (Italy) WHITMAN
Austria MOTON (Germany). Autonics (Korea), Delta (Taiwan).
More than enough manufacturers of shopping malls in Russia. These are
companies such as Aries LLC Elemer, Thermodat, Teplopribor, MZTA, Vibrator,
Danaterm, NPP Avtomatika, Sensorika, FEA, Kontravt and many others. Only a
few dozen, although the Aries is the undisputed leader who is difficult to
compete with. In Ukraine, the production of thermal controllers is carried
out by LLC MIKRA (Kiev), Scroll (Ivano-Frankivsk), Prompribor in Zhytomyr,
Terra in Chernigov, a branch of the Russian Aries in Kharkov and several
others. In general, about a dozen.
As for the Chinese controllers, the skepticism towards them is very
great. In Russia they are not bought even in the Far East, where they are
even cheaper due to the proximity of delivery. At the same time, it is not
uncommon for controllers of Russian or Ukrainian production to put on imported
production lines, since they are quite competitive in a number of
respects. The only problem is that the models announced by dealers may not
be in stock.
Maxim Krets, head of the assortment of instrumentation and automation of
OVEN company (Russia, Moscow): “Not all manufacturers of polymer products use
imported equipment, although if we talk about manufacturers of local
automation, the share of imported equipment is, of course,
overwhelming. Nevertheless, in Russia there are domestic manufacturers of
injection molding machines, extruders, etc. The attitude to the domestic
product is often biased, but in fact it turns out that working with the
domestic manufacturer is sometimes easier, and there are enough reasons:
quite decent quality;
the price is lower than that of European counterparts;
shorter delivery times;
availability of technical support and service.
A number of targeted state programs also affect the situation, due to which
suppliers are limited in the use of imported equipment. And this fact
contributes to the promotion of domestic products.
Very different numbers in the price range of equipment. The Europeans have
the so-called "top line" - they are ten times more expensive. Lines of
mid-range appliances are about 3-5 times more expensive, Japanese-made products
are 1.5-2 times more expensive, and Korean ones are cheaper. China is not
even discussed due to the unacceptable quality of equipment in this category
...
Problems with the replacement of failed equipment are, in principle, possible, although they are primarily technical in nature. If it is necessary to carry out an optimal replacement, the difficulty most likely consists in correctly formulating the tasks that automation should perform. But the implementation itself does not raise questions.
There are enough competitive companies producing TK in Russia. These are Elemer, Thermodat, Teplopribor, MZTA, Vibrator, Danaterm, NPP Avtomatika, Sensorika, FEA, Kontravt and many others. "They are opposed by such well-known world leaders as Yumo (Germany), Omron (Japan), Autonics (Korea), Delta (Taiwan)."
Alexey Balykin, Director of Sitron-KIP LLC (Russia): “Our company is a direct manufacturer of equipment, and this equipment is in high demand among Russian enterprises operating in the polymer industry. We produce ready-to-operate controllers using instruments and sensors manufactured by Aries LLC. As for competition in this area on the Russian market, the situation here is dictated by the fact that if someone prepares production from scratch, it is likely that the entire production line will be equipped with thermal controllers of the same manufacturer as the main production line.
But I would not say that imported devices completely dominate the Russian market. This is due to both a significant difference in cost and difficulty in maintenance. If an imported thermal controller fails, then its repair in Russia is fraught with considerable difficulties. In principle, shopping malls of foreign manufacture can be repaired in Russia as well, but this requires significantly more time, especially when it comes to replacing parts that take a long time to deliver. Our controllers are consumed, of course, mainly in Russia, since there are significantly fewer plastic processing enterprises in other CIS countries. Recently, we remember only two deliveries of shopping malls to Ukraine and Belarus. ”
The degree of demand and problems of operation
Initially, the controller as equipment is not bought as often as suppliers and
manufacturers would like. This happens when a new production is created or
something is going down on the existing one. The controller can work for
years up to the obsolescence of equipment, if properly operated. Alas,
unskilled intervention can ruin any controller. According to "PD" Yuri
Shovgenyuk, most of the devices that are returned for repair were damaged or
burned by unskilled personnel. Unfortunately (and maybe, fortunately for
suppliers and manufacturers), the controller's lifespan is most dependent on
the human factor. Statistics show that 95% of TC breakdowns are the result
of low-skilled operators.
The same opinion is shared by Maxim Batsenko: “Unfortunately, we still have to pay attention to the low production culture and the lack of understanding by many manufacturers of why thermocontrollers are needed in the line. We still have a shortage of qualified personnel and a low level of production culture. And here the problems are approximately equal both in Russia and in Ukraine. The standard situation is when the thermal controller is remembered at the time of equipment startup. And most often this happens at new injection plants, since for TPA the thermocontroller is a desirable, but not obligatory option. Using a temperature controller allows you to reduce the loss of raw materials at startup, improve stability, and also get better products. It is easier with extrusion - as a rule, thermocontrollers are included in the composition of the line. ”
Extremely undesirable for these devices are also surges in the network, which are typical for our enterprises. Because of this, precision electronics “flies” and sensors burn out. Powerful equipment operates at industrial enterprises, and therefore surge surges at our enterprises are commonplace. So, dealers to a large extent owe not only to illiterate personnel, but also to our power engineers. And I would like the number of sales to be provided by increasing volumes of production ...
Konstantin Egorov
Article from the magazine Polymers-Money, August 2011