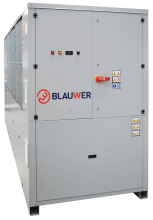
FREE STANDING VISION SORTING SYSTEM for PRECISION INSPECTION of PLASTIC CLOSURES
100% inspection and sorting of plastic closures up to 3000 pieces per minute
Caps are fed to the sorter oriented in single file. The conveyor and spacing unit have adjustable speed control and are able to present caps evenly spaced at 3000 pieces per minute.
The precision spacing unit and tracking system ensures that the parts are presented to the cameras within less than 0.5 mm position variation in any direction, granting consistent inspection. The caps are inspected by the camera system.
Bad parts are blown off the belt by the Solenoid controlled Reject Mechanism.
Cap Sorter includes:
Features:
High resolution All Surface Cap Inspection
2x Overhead Camera
4 x Side Camera
Side & Internal Surface Inspection
External Dimension Testing
Data Client
ideal data client logs data, images and events to a local server or network
(multiple servers).
The system logs production data by month, day, shift, hour, production lot.
User interventions such as model resets, setting changes, alarm resets are all
recorded by date, time and user.
Vector Analysis
Vector Analysis is a unique inspection algorithm which allows unskilled operators to AUTOMATICALLY SET system with the highest precision inspection capability. The system creates an Ideal Vector Model using a sample set of good samples. This models the natural variation of both colour intensity and gradient orientation features on the good parts. Any feature which is not present in the model is detected as a defect. The key benefit of the Ideal Vector Analysis is the ability to detect anomalies on highly contoured surfaces, repeatedly detecting defects in areas that traditional vision systems cannot match. If there are variations in material, which may occur in different production runs, it is simply a case of adding samples to the model to include these variations. The user can define inspection zones based on the Vector Model allocating the zones with 3 different sensitivity levels. These are general sensitivity levels which apply the same inspection capability to all zones on the same level. So there is no need to set sensitivity specifically for lots of different zones. The sensitivity level are intuitive and easy to set using simple slider bars.
Colour Intensity and Orientation Vector Model
External flashing Missing flag
Wavy flange Contamination
Liner flashing
The above examples demonstrate the systems capability to detect defects on irregular Contours
Precision Measurement
Multi point dimension test measures critical dimensions repeatably within <0.2 pixel. On 30 mm diameter closures this is approximately 20 mm.
Imaging
Fish Eye overhead camera for inspection of Base Inner, Sidewall and Tamper Band Surface. Tele-centric overhead camera for dimension measurements. Side View multi camera for inspection of external side wall and tamper band. Multi Camera also allows side dimension measurement. Therefore the multi camera provides extremely high capability for sorting of small vertical flashing and tamper band defects.
General Detection Specifications for all Types of Beverage Closures
Moulding Defects
|
|
Liner Defects > 100 mm2
|
|
Dimension Testing • Accuracy •±25mm
|
|
---|---|---|---|---|---|
Horizontal Flashing | X | Liner Void (under-fill) | X | Outer Diameter | X |
Vertical Flashing | X (50mm) | Liner Flash (over-fill) | X | Seal Diameter | X |
Missing Flags | X | Clipped Liner | X | Ovality | X |
Smileys (lifted tamper band) | X (50mm) | Misplaced Liner | X | Height | X |
Deformation | X | Double Liner | X | Tamper Band (width) | X |
Pulled Thread | X | Contamination | X | Bulge (width) | X |
Short Thread | X | Knurling (width) | X | ||
Cracks | X | ||||
Contamination Internal | X | ||||
Contamination External | X (50mm) | ||||
Colour Variation | X |
Specification Sheet
|
|
---|---|
PC | I2S Industrial Intel i7 platform |
Data Storage | Solid State (no Hard Drive) |
OS | Windows 7 |
Cameras | Digital IEEE 1394b |
Illumination | Solid State Cool White |
Rejection Mechanism | Blow Off Solenoid |
Maximum Inspection Speed | 3000 pieces per minute |